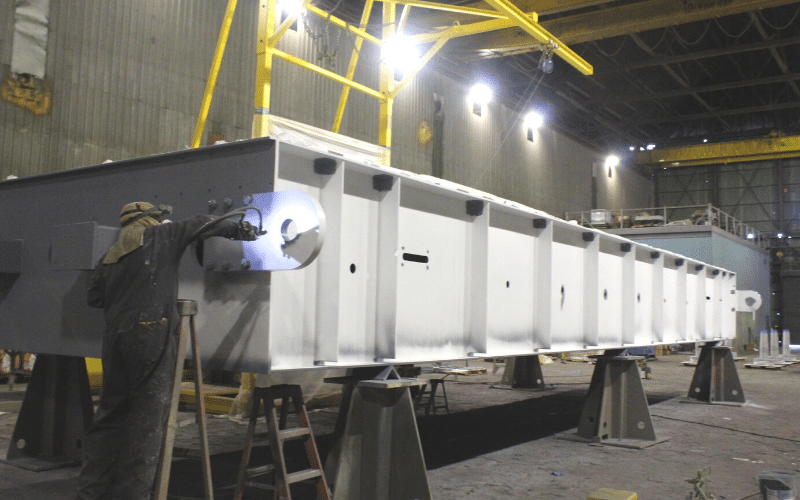
Production workers in Oregon will soon have a pathway to better training and more job opportunities thanks to Local 16’s new state-registered production apprenticeship program, a long-gestating idea that will help workers in the manufacturing sector for years to come.
The new program will be a two-year apprenticeship, with five weeks of intensive daytime training each year, administered by the Local 16 JATC.
“We saw a need for an apprenticeship for our production shops,” said Local 16 Regional Manager Brian Noble. “We wanted to get training for members so they could always improve themselves and be more qualified and skilled for signatory contractors.”
Local 16 Regional Representative Darrin Boyce explained that Local 16 had an extraordinarily strong production membership in the 1980s, but thanks in part to the trade policies of President Ronald Reagan, he argued, and the North American Free Trade Agreement (NAFTA) later on, the manufacturing sector was decimated, leading to decline. In addition, until a few years ago, Local 16 representation for production workers was siloed off from that of the building trades, with different officers assigned to different shops.
“You don’t have the shared resources, you’re not bouncing ideas off of each other,” Boyce said. “So [Noble] decided to break up [that siloing].”
It didn’t take long for elected officers to realize that many of the issues production workers raised during bargaining could be addressed through formalized training that spoke to members’ needs — in other words, a state-registered program that helped workers achieve guaranteed wage rates, assisted contractors with securing work opportunities and helped SMART members build their skills.
Noble noted that a state-registered program that meets Oregon’s established labor standards is especially important right now. By going through the apprenticeship program, Local 16 production workers and contractors may be able to secure work in the burgeoning offshore wind industry.
“In Oregon, we have labor standards set up for any of the offshore wind platforms, and the development for offshore wind, [that include] apprenticeship requirements,” he said.
Coming up with a state-registered production apprenticeship program was one thing. Creating it was another.
“Some of the challenges were getting our contractors on board with adding contributions in their contracts to the JATC,” Noble said. In other words, employers who previously hadn’t provided funding for training needed to see that there would be bang for their buck.
“We ended up bringing the contractors to the table to be like, ‘hey, what kind of training would you guys want?’” said Boyce. “And so really what we’re looking at is having the last year [of the apprenticeship program] being tailored to each shop.”
Local 16 also needed to work with the Oregon Bureau of Labor and Industries to ensure the program met all the criteria to be state registered and to structure the apprenticeship in a way that benefited members. Because production workers have different daily schedules and demands compared with building trades members, making evening instruction a more difficult task, Local 16 designed the production apprenticeship to not only meet the high standards set for state-registered apprenticeship programs, but also to allow members to collect unemployment pay while they attend the five-week course. (Oregon law allows apprentices in state-registered programs to do so, Boyce said.)
The apprenticeship program is becoming reality. Now, Noble and Boyce think it could benefit Local 16 members for the long term — whether from offshore wind project work, day-to-day job satisfaction, Local 16’s market share or all of the above.
“The direct benefit for members is a pathway to that higher-wage position in the facilities they work in, with a guaranteed timeline and a direct path that isn’t just at the whim of the contractor,” Noble said. “I also think it’s an opportunity for us to organize more production facilities.”
“We know why union is better, and that is the quality,” added Boyce. “You’re not going to have a high turnover rate. You’re going to have lifelong workers, dedicated, that are going to be making the company a lot of money. And one of the ways to show them that is with a good, state-registered apprenticeship program where we have qualified people and we’re giving them the training that specifically addresses their needs.”
Related News
- “Organizing is our lifeblood:” Benson details the role every member plays in strengthening SMART
- “Three Pack” attacks: SMART councils meet to fortify union in California
- Local 540 members sew union pride into SMART apparel
- Local 435 lifts working conditions, pay and benefits in Gainesville
- Local 480 drives unprecedented growth at Daikin in Southeastern Minnesota
- SMART statement on passage of Inflation Reduction Act
- SMART statement on passage of CHIPS and Science Act
- SMART Education Department holds organizing training in Portland